~就活室便り~#19 和歌山から世界へ 島精機製作所様訪問記
みなさんこんにちは。就活室のHANAZONOです。年も改まり、今回が2025年最初の
就活室便りになります。ファッション業界のあれこれを、少しでもわかりやすくお伝え
できたらと、本年も頑張っていこうと思います。写真が見にくいというかはっきり言って
下手だとか、調子に乗って文章長すぎ、とかいろんな弱点は承知してはいるのですが、
まあ本人なりにいろいろ改善は心がけていて、なるべく表現も簡潔に、写真も文章も
丁寧に、を意識しつつどこまで改善できるかわかりませんが、それでも性懲りもなく
レポートは続けていきますので、よろしくお願いします。
以前にも報告させて頂いた島精機製作所様のApex Fizですが、今回は学生とともに実際に
お邪魔して、講習と実演をしていただきました。
まずホールガーメント(無縫製ニット)の説明からしていただきました。現在この編機を
生産しているのは世界で島精機製作所様だけです。今回の説明では編機生産は全て本社
和歌山の工場で行っているそうです。特にそのことには言及されませんでしたが、世界中の
産業が、工賃が安い、コストの問題で海外生産に依存し、その結果、生産技術が大量に
生産国に流出したことがありました。いずれにしろ相手に設計図を渡す、ということは
そういうことだど思います。以前、婦人コートを生産していた時に、来シーズンのサンプルを
海外工場に依頼し、その1か月後その国で開催された総合展示会を訪問したところ、少なく
とも10社からその形が自社の新商品としてブースに飾られていました。特に独自の技術の
商品を生産する場合、海外生産にはやはり技術漏洩のリスクがあると思います。もっとも
それは国によってかなりの差はあることは確かですが、いずれにしろ世界一の生産大国を
さらに自国の技術を流出させて繁栄させることもないですよね。
ホールガーメントは例えばユニクロさんでは3Dニットの名で呼んでいたり、各社いろいろ
名前は付けていますが、その編機自体はすべて島精機製作所様作成のものです。小ロッド
生産にも対応でき、裁断、縫製がないため繊維くず、裁断くずが出ず、縫い目がないため
縫い代擦れが起こらず、ウェアだけでなく下着でもそしてベビーウェアでも重宝されて
います。
そしてスタートのスイッチを押す以外人間のすることはあまりないので最低限の人員で
工場を回すことが可能です。
無人化、省力化が進んでも従来の糸、生地の試染、試織、1stサンプル、各色サンプルの作成、
サンプル修正はなくなったわけではなく、それがコストやリードタイムの圧迫につながり
ます。それを解決していくのがApex Fizというシステムになります。
これは前回紹介させていただいたとおり、色、柄等を素材、デザインに合わせて表現していく
システムです。このシステムを使用してプリントアウトしたものはまさしく生地と紙との見分け
がつきません。下が、学生たちがその真贋探しをしているところです。
各色のスワッチのうち一つだけがリアルの生地なんですけどみんな必死に本物探ししていました。
ソフトとしてはillustratorに近いものだと思うのですが、画面を修正し新しい柄に置き換える、
という作業が衣服に特化しているだけに格段にやさしく行えます。
モデルが着ている服だけ切り取り、そこから袖だけまた切り取り各パーツごとに字の目を設定、
元の写真からドレープ、しわなどの部分の陰影をスポイト(、というように呼ばれていたので
そのようなツールの名前なんだと思います)で吸い取り反映させると、元のドレープ、結び目、しわ、
等すべて再現できます。それがまた短時間でマウスの操作だけで行えるため、illustratorのように
熟練する必要はないようです。さらにCADとの連携、グレーディング、柄ピッチの変更、別の編地柄の
挿入、等が行えるので、バーチャルサンプルを作ることが可能です。ウェア本体カラーもパントーンの
色はプリセットされているのでそこから選択可能、写真を読み込んだ場合はそれからから一番近い
パントーンのカラーを自動的に表示することが可能、付属に関してもYKKのカラーがプリセットされて
いるため表地に合うものを画面で選び、そのまま付属として発注することができ、サンプル作成の
省力化、リードタイムの削減、無駄を極限まで省くことができます。
このソフト自体は学校でも月額料金で使用できるためいつかは学校での必修科目となる日が来るかも
しれません。そして、アパレルメーカーでは操作が必須になっているところも出てきているようです。
ロスの排除の意味も大きいですが、なによりリードタイムの減少が一番大きいかな、と思いました。
以前はニットの新製品を作ろうとしたら、デザイン・パターン作成→糸の決定→糸ビーカーの作成
(本番の染に入る前に、本番は釜で染めますが、見本としてまず少量ビーカーで染めます)→色確認
→糸染め→ファーストサンプル→各色サンプル、という順番で作業を進行します。各工程ごとに訳1か月の
納期、そこで修正が入るとさらに1か月遅れます。企画が始まってから最低でも半年、下手すると1年、
そこから本生産を開始すると、企画段階から早くて1年、というのが従来の納期です。それがデザインさえ
決定していれば1か月程度でその全工程を終え、本生産に入れることになります。気候、流行ともに変わり
やすい現在の状況の中で、このリードタイムの縮小はかなり大きな意味を持ちます。
ものづくりの面からみて画期的なこのシステムは販売の面でも画期的な効果をもたらします。既にこの
システムを導入している会社を数社紹介して頂きました。大手シャツ、ネクタイ製造販売の企業様の
導入例を紹介していただきましたが、webカタログにネクタイが100柄近くあります。その写真はすべて
合成だそうです。当然シャツもすべて合成。製品の陰影まで再現できるため全く合成とは気が付きません。
大手アパレルの製品もサンプル作成は1型1色だけ、あとは全て合成だそうです。ネクタイ100本いちいち
結び目を作って撮影していたら一体何時間かかるでしょう。それがすべて1クリックでできてしまいます。
近年ECで最も手間のかかる作業が俗に言う「ささげ」(採寸、撮影、原稿―紹介文作成)と呼ばれる作業で、
この作業にとられる手間の膨大さに各社頭を悩ませていました。その手間が、少なくとも三分の一になる
のです。これはメリット、というよりは革新に近いと思います。
そんな講義を受けた後、そうして作られたホールガーメントの製品を見学させていただきました。
ホールガーメントは無縫製、縫い目がないため、ニットのシルエットがより柔らかく表現できます。元々
製品が立体でできているのと相まってドレープ性はかなり豊かですね。
写真ではわかりにくいかもしれませんが(今年はもう少しうまく写真が撮れるようにしたいです)、中央
テーブルの上のGジャンは実は刺繍ではなくプリントです。顔料プリントで少し立体感があるため本物と
さらに区別がつきにくいです。解説されてみれば確かにデニムの縫い目は厚くてそこに刺繍は無理なんです
よね。騙された、というより本当によくできています。
というように今回は1年生を連れて訪問させて頂きました。かれらにとっては今回が初めての企業訪問、
見学で、思った以上に緊張してたり興奮したりしたようです。今回の技術に興味を持っていいただきたい
のはもちろんですが、こうしてファッション産業の裏側には様々な企業、様々な人たちが独自の技術を競い、
支えているからこそ華々しい表舞台がある、ということを少しでも学んでいただけたらな、と思います。
そして裏側の領域は想像以上に奥行きがあり、そんな世界に1人でも関心を持ち進んでくれたらな、と思い
ます。ファッションの表舞台、ブランドは圧倒的に海外のものが多く、ライセンスを含めると日本独自の
ブランドは海外ブランドに対し、優位に立っているとは決して言えません。しかし、素材や特に技術部門に
関しては現在むしろ海外で引っ張りだこです。ユニクロさんの匠制度もそうですが縫製技術指導だけでも
どれくらいの日本人が海外で働いていることでしょう。今後もこんな技術を世界に誇っていけたらと思います。
去年の年末に1年生とお邪魔した島精機製作所様のレポートをお届けしました。このレポートが公開されて
いる時間には、実は2年生を連れてお邪魔しているところです。また新しい発見があればレポートさせて
頂きます。
ではまた。
HANAZONO
★★★★★★★★★★★★★★★★★★★★★★★★★★★★★★
東京服飾専門学校 次回オープンカレッジの日程
1/19に開催予定です。
詳しくは下記よりご確認ください。
https://www.tfac.ac.jp/open_college/
【Web学校見学を随時受け付けています】
授業見学のご予約は下記URLから予約フォームでお受けしています。
https://www.tfac.ac.jp/学校見学予約カレンダー/
♦資料請求・学校見学・WebオープンカレッジがLINEで簡単に
申込ができるようになりました。
お友達追加お願いします♪♪
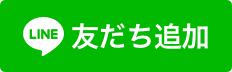
♡tfac Instagramフォローお願いします♡
@tfac__official

★★★★★★★★★★★★★★★★★★★★★★★★★★★★★★